1、工艺性质不同
1. Different process properties
干法工艺是指那些在脱硫过程中烟气始终保持干态的工艺,除了炉内喷钙外,都要求以生石灰作为吸收剂。湿法脱硫原理是指在脱硫过程中烟气处于或部分时段处于饱和状态的工艺,用于湿法的吸收剂主要是石灰石,氨、氧化镁等也可用来作为吸收剂。
Dry process refers to those processes that keep the flue gas dry during the desulfurization process. In addition to calcium injection in the furnace, quicklime is required as the absorbent. The principle of wet desulfurization refers to the process in which the flue gas is saturated or partially saturated during the desulfurization process. The absorbent used for wet desulfurization is mainly limestone, and ammonia, magnesium oxide, etc. can also be used as absorbent.
2、技术特点不同
2. Different technical characteristics
湿法脱硫技术指的是,反应剂在浆液状态下进行脱硫和脱硫产物的处理。湿法脱硫的主要设备包括喷淋塔和液柱塔脱硫系统;干法脱硫工程是指以石灰为脱硫吸收剂,采用喷雾形式进行脱硫处理。在吸收塔内,被消化并加水制成的石灰鲁剂被雾化成细小液滴,与烟气混合接触,使烟气中的SO2发生化学反应成CaSO3,烟气中的SO2被脱除。
Wet desulfurization technology refers to the treatment of desulfurization and desulfurization products by the reaction agent in the slurry state. The main equipment of wet desulfurization includes spray tower and liquid column tower desulfurization system; The dry desulfurization project refers to the desulfurization treatment in the form of spray with lime as the desulfurization absorbent. In the absorption tower, the lime slurry which is digested and added with water is atomized into small droplets and mixed with the flue gas to make the chemical reaction of SO2 in the flue gas into CaSO3, and the SO2 in the flue gas is removed.
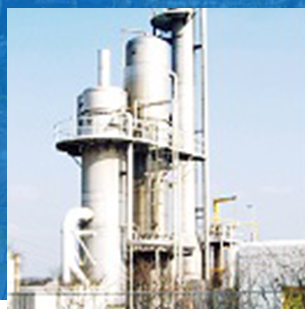
3、成分原料不同
3. Different ingredients and raw materials
干法脱硫剂的主要成分是生石灰和水配制成的乳状脱硫剂(氢氧化钙)。湿法脱硫主要利用石灰石或石膏浆液洗涤烟气,使其与SO2反应生成亚硫酸钙(CaSO3)。分离的亚硫酸钙可以被废弃,或者可以强制进入空气中氧化,并且可以添加一些添加剂以石膏形式回收
The main component of dry desulfurizer is the emulsion desulfurizer (calcium hydroxide) prepared by quicklime and water. Wet desulfurization mainly uses limestone or gypsum slurry to wash flue gas and make it react with SO2 to generate calcium sulfite (CaSO3). The separated calcium sulfite can be discarded or forced into the air for oxidation, and some additives can be added for recovery in the form of gypsum
4、吸收剂不同
4. Different absorbents
干法脱硫使用的吸收剂可分为钙基和钠基两种,吸收剂可以是干的、湿的或浆状的。烟气在反应器中照射后,烟气分解产生大量的氢氧和氧原子,促进烟气中二氧化硫和氮氧化物生成硫酸和硝酸,再与氨水反应,形成硫酸铵和硝酸铵的混合物,用作农用肥料。
The absorbents used for dry desulfurization can be divided into calcium base and sodium base. The absorbents can be dry, wet or slurry. After the flue gas is irradiated in the reactor, the flue gas decomposes to produce a large number of hydrogen and oxygen atoms, promoting the formation of sulfuric acid and nitric acid from sulfur dioxide and nitrogen oxides in the flue gas, and then reacts with ammonia water to form a mixture of ammonium sulfate and ammonium nitrate, which is used as agricultural fertilizer.
湿法脱硫一种是采用吸收性能好、易于再生的氧化镁作为吸收剂吸收烟气中的SO2。采用两个除尘器串联,以除去烟气中的小粉尘颗粒,再生后的氧化镁可以作为吸收剂再利用;另一种是以氨水为吸收剂,吸收烟气中的二氧化硫,其中间产物为亚硫酸铵和亚硫酸氢铵。采用不同的方法处理中间产物,回收硫酸铵、石膏、单体硫等副产物
One kind of wet desulfurization is to use magnesium oxide with good absorption performance and easy regeneration as absorbent to absorb SO2 in flue gas. Two dust collectors are connected in series to remove small dust particles in the flue gas. The regenerated magnesium oxide can be reused as absorbent; The other is to use ammonia water as absorbent to absorb sulfur dioxide in flue gas, and the intermediate products are ammonium sulfite and ammonium bisulfite. Use different methods to treat intermediate products and recover by-products such as ammonium sulfate, gypsum and monomer sulfur
5、性价比不同
5. Different cost performance
湿法脱硫反应速度快,效率高,技术比较成熟,生产运行安全可靠,始终占据主导地位,但产生的生成物较难处理,能耗高,占地面积大,设备庞大。干法脱硫相对于湿法脱硫来说完全相反,设备简单,占地面积小,投资运行费用较低,操作方便,能耗低,生成物便于处置,无污水处理。
Wet desulfurization has fast reaction speed, high efficiency, relatively mature technology, safe and reliable production and operation, and always occupies the leading position, but the generated products are difficult to treat, high energy consumption, large floor area, and huge equipment. Compared with wet desulfurization, dry desulfurization is completely opposite, with simple equipment, small floor area, low investment and operation costs, convenient operation, low energy consumption, easy disposal of products, and no sewage treatment.